- Pubblicato il 1 set 2023
- Ultima modifica 1 set 2023
- 6 min
Il modulo a basso consumo energetico che riduce il consumo di aria compressa
Unilever lavora per ridurre l'utilizzo di aria compressa nei componenti pneumatici grazie al modulo innovativo MSE6-E2M. Vediamo di cosa si tratta e come funziona.
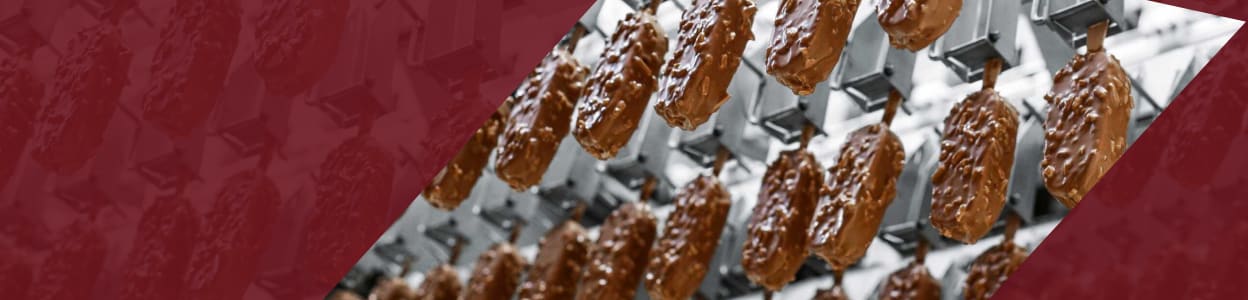
Unilever, una società globale nota per il suo impegno verso pratiche di risparmio energetico, sta compiendo passi significativi per ridurre l'utilizzo di aria compressa nella produzione dei gelati Magnum. Implementando il modulo innovativo di efficienza energetica MSE6-E2M, l'azienda mira a mantenere la sua filosofia di Optimizing Pleasure Minimizing Usage anche nel processo produttivo.
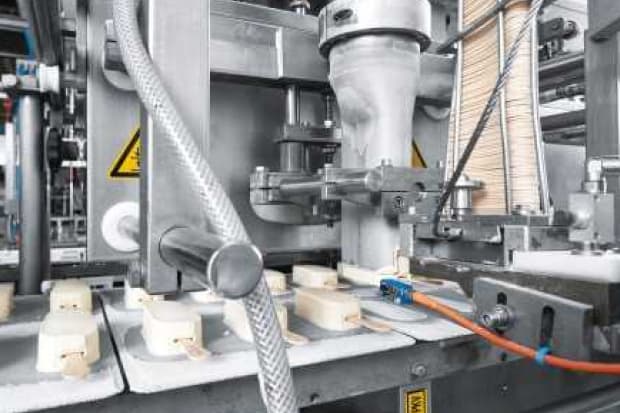
Sebbene il gelato sia rinomato per le sue qualità rinfrescanti e la miscela energizzante di proteine e carboidrati, il processo di creazione di questa deliziosa leccornia richiede un considerevole consumo di energia. Dal miscelare latte, cioccolato al latte, zucchero e fave di vaniglia, al congelamento a -25 °C, all'immersione in vari rivestimenti di cioccolato e all'imballaggio finale, l'elettricità e l'aria compressa sono fondamentali per i processi termici e cinetici coinvolti. Unilever riconosce l'importanza dell'efficienza energetica e l'ha posta come una priorità assoluta. Attraverso il Piano di Sostenibilità di Unilever, l'azienda ha già raggiunto oltre 150 milioni di euro di risparmi energetici grazie a miglioramenti nell'efficienza produttiva dal 2008.
Nel campo della pneumatica, Unilever riconosce il potenziale per il risparmio energetico e la riduzione dei costi attraverso innovazioni avanzate. Recentemente, presso lo stabilimento Unilever a Heppenheim, è stato implementato con successo il modulo di efficienza energetica MSE6-E2Mper ridurre il consumo di aria compressa nella produzione dei gelati Magnum. La collaborazione tra Unilever e Festo nel portare questo modulo di efficienza energetica dalla fase di prototipo alla produzione ha sottolineato anche il concetto che meno è più, non solo in termini di consumo energetico, ma anche in altri aspetti del processo.
Sostenibilità lungo tutto l'intero processo
Lo stabilimento di Heppenheim di Unilever svolge un ruolo importante come centro di produzione per il gelato, inclusi i prodotti più popolari della linea Heartbrand come Magnum, Feast, Viennetta e Carte d'Or. La capacità dello stabilimento di produrre grandi quantità è essenziale per soddisfare la domanda in varie parti del mercato europeo. Tuttavia, questo livello di produzione richiede una quantità significativa di energia.
Unilever ha riconosciuto l'importanza di ridurre il consumo di aria compressa nei componenti pneumatici per migliorare la sostenibilità. La sfida consisteva nel visualizzare e misurare l'utilizzo di aria compressa, poiché il consumo delle singole linee di produzione non era stato determinato in precedenza. Alexander Hemmerich, un ingegnere di automazione presso lo stabilimento Unilever di Heppenheim, ha dichiarato: "Fino ad allora eravamo all'oscuro. L'aria non è visibile, quindi non è immediatamente evidente se il consumo è troppo elevato." Nell'ambito del Piano di Sostenibilità di Unilever, lo stabilimento di Heppenheim aveva già ottenuto successi in altre aree. Hanno sostituito motoriduttori a basso rendimento con alternative più efficienti, ottenendo risparmi energetici fino al 60%. Inoltre, hanno convertito numerosi ventilatori da 18 kW nei tunnel di raffreddamento utilizzando convertitori in frequenza con coppia quadratica.
Questa conversione ha portato a una riduzione del consumo energetico di circa il 40% per i ventilatori. Ponendo l'accento sulla sostenibilità lungo l'intera linea di produzione, Unilever sta compiendo passi significativi per ridurre il suo impatto ambientale e promuovere pratiche di produzione responsabili.
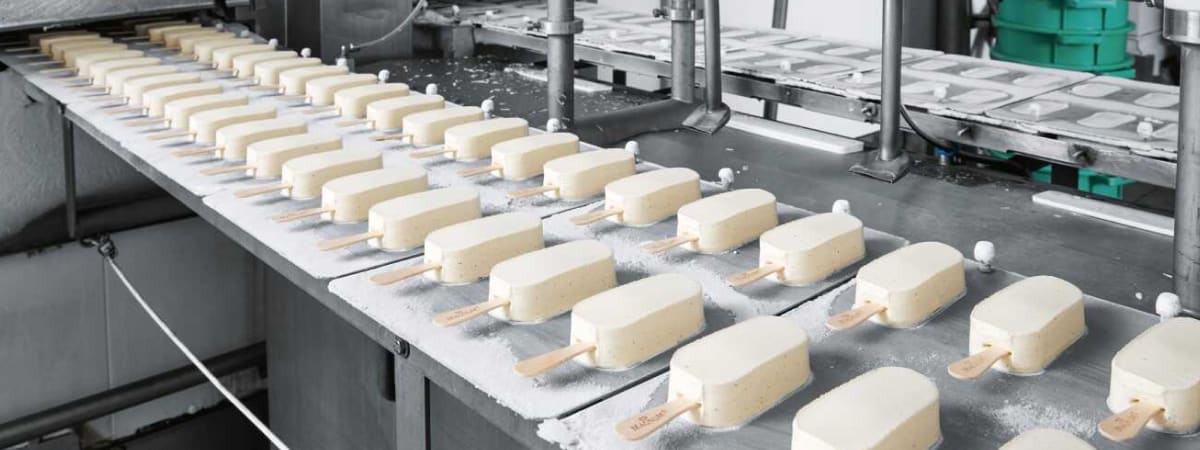
Monitoraggio del consumo energetico
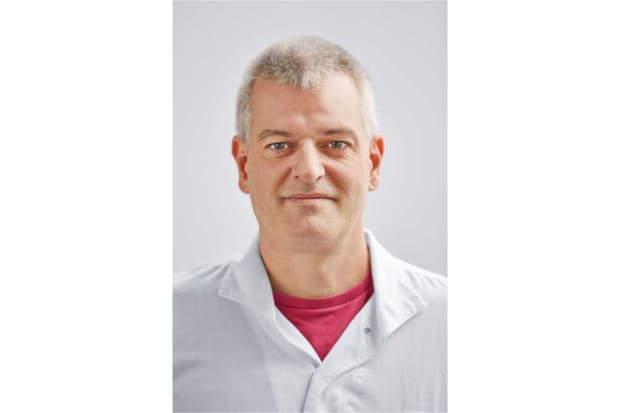
Il consumo energetico diventa visibile attraverso l'implementazione del modulo di efficienza energetica MSE6-E2M di Festo, un passo significativo intrapreso da Hemmerich e dal suo team per ridurre l'utilizzo di aria compressa. Hemmerich ha spiegato che il modulo forniva loro la possibilità di monitorare la quantità di aria compressa utilizzata durante il funzionamento di una linea di produzione. Spegnendo singoli consumatori, potevano identificare le variazioni delle esigenze di aria compressa, individuare le perdite ed eliminare il consumo superfluo.
La funzione di spegnimento automatico del MSE6-E2M in modalità di standby consentiva loro di determinare quanto velocemente si svuotava il sistema, evitando anche un ulteriore consumo di aria compressa quando il sistema non era in funzione. Il modulo notificava tempestivamente al controller di sistema qualsiasi calo di pressione insolitamente rapido. Inoltre, il MSE6-E2M possedeva intelligenza integrata e un modello specifico per il funzionamento dei sistemi ad aria compressa, consentendogli di riconoscere autonomamente quando un sistema era in produzione o in fase di fermo. Tuttavia, presso Unilever, il MSE6-E2M era gestito attraverso il controller di sistema per consolidare tutte le informazioni in modo centralizzato.
Consumo energetico di aria compressa significativamente ridotto
Implementando il monitoraggio delle condizioni per i componenti pneumatici del macchinario del Magnum, Alexander Hemmerich ha ottenuto accesso a dati continui, rilevanti per il processo. Il MSE6-E2M comunicava regolarmente con il controllore della macchina tramite Profibus importanti parametri di misurazione come flusso, pressione e consumo. L'utilizzo del modulo era comodo attraverso il pannello di controllo. Hemmerich ha sottolineato che il modulo di efficienza energetica di Festo permetteva loro di ridurre gradualmente il consumo di aria sulla linea di produzione dei Magnum. Inoltre, la connessione Profibus eliminava la necessità di cavi aggiuntivi durante la conversione dei sistemi esistenti. Di conseguenza, la linea di produzione dei Magnum ha visto una riduzione di oltre 500 euro all'anno dei costi di consumo di aria compressa.
Gli elementi essenziali del modulo di efficienza energetica MSE6-E2M

Il prototipo del MSE6-E2M è stato sottoposto a test sul campo nella linea di produzione Magnum di Unilever, offrendo un ambiente ideale per la valutazione. La stretta collaborazione con gli sviluppatori di Festo e il suo utilizzo pilota presso lo stabilimento di Heppenheim hanno svelato importanti requisiti operativi. Di conseguenza, la versione finale del modulo di efficienza energetica, MSE6-E2M, è stata perfezionata per adattarsi meglio alle operazioni quotidiane.
In risposta allo spazio di installazione limitato nei sistemi esistenti, il MSE6-E2M è stato progettato per essere compatto, con priorità all'efficienza energetica. Di conseguenza, gli slot I/O della versione iniziale sono stati sostituiti con un'interfaccia Profibus. Inoltre, è stata eliminata la valvola di scarico presente nel prodotto di prima generazione. Queste modifiche hanno permesso di sviluppare il MSE6-E2M come una combinazione di sensore di pressione e flusso, una valvola di intercettazione e un nodo Fieldbus.
Ora disponibile come prodotto commerciale, il MSE6-E2M ha circa la metà delle dimensioni del prototipo, rendendolo perfettamente adatto per gli operatori e i costruttori di macchine. Semplifica e migliora il monitoraggio dell'energia, supportando aziende come Unilever nei loro sforzi per aumentare in modo efficace la sostenibilità.
Il modulo di efficienza energetica MSE6-E2M funziona autonomamente, monitorando e regolando l'alimentazione di aria compressa sia nei nuovi sistemi sia in quelli esistenti. Simile a un sistema di start-stop in un'automobile, questo modulo intelligente rileva le modalità di standby e interrompe automaticamente l'alimentazione di aria compressa.
Di conseguenza, il consumo di aria compressa si riduce a zero durante le fasi di inattività e le pause del sistema. Inoltre, il MSE6-E2M consente la rilevazione delle perdite avvisando gli operatori di sistema se la pressione scende troppo rapidamente durante le fasi di inattività. Inoltre, fornisce continuamente dati essenziali per il processo come flusso, pressione e consumo, che vengono trasmessi al controllore della macchina tramite Profibus.