- Pubblicato il 23 feb 2024
- Ultima modifica 23 feb 2024
- 5 min
RAMS: le migliori tecniche per valutare le proprie apparecchiature
L’analisi RAMS è uno strumento di valutazione dettagliata per stimare la durata delle apparecchiature, prevenire i guasti e ridurre i costi di manutenzione. Ma in cosa consiste esattamente?
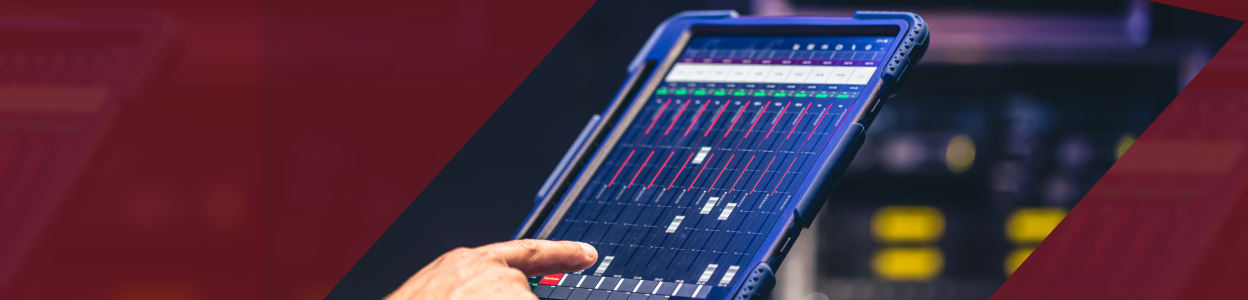
L’analisi RAMS è uno degli approcci tecnici più utili per valutare lo stato di salute delle proprie apparecchiature. Vero e proprio pilastro dell’ingegneria della manutenzione, il suo acronimo unisce quattro indicatori (affidabilità, disponibilità, manutenibilità, sicurezza) che permettono di stimare la durata delle apparecchiature, di prevenire i guasti e di ridurre i costi di manutenzione e dei ricambi.
Il risultato è un atteso miglioramento della produttività, della redditività e della competitività dell'azienda.
Analisi Rams: cos’è e quali sono i suoi obiettivi?
Come già accennato, RAMS è l'acronimo di affidabilità, disponibilità, manutenibilità e sicurezza (in inglese, Reliability, Availability, Maintainability, Safety), quattro elementi che possono ben farci comprendere quanto sia importante focalizzare l’attenzione dell’organizzazione sulle caratteristiche qualitative delle proprie apparecchiature.
Tuttavia, per valutare compiutamente le finalità, è bene partire con la definizione dei suoi obiettivi e dei benefici, oltre che delle modalità di implementazione.
Si ricorda infatti che gli obiettivi dell'analisi RAMS sono:
- la riduzione dei costi di manutenzione e di funzionamento
- il miglioramento della produttività
- la crescita dei profitti.
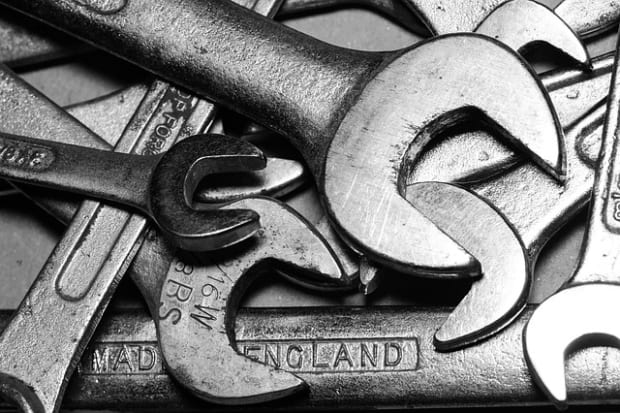
Ebbene, per coglierli l'analisi RAMS valuta le prestazioni del sistema misurando il numero di guasti, il tempo che intercorre tra un guasto e l'altro e il tempo necessario per ripararli, oltre ad altre metriche: utilizza così dei calcoli e dei numeri per valutare le apparecchiature, e dunque esprime in termini quantificabili i suoi risultati.
Analisi di affidabilità (Reliability)
La prima lettera di RAMS rappresenta l’affidabilità, intesa come la probabilità che la macchina svolga la sua funzione per un determinato periodo di tempo. Il dato, che monitora i tassi di guasto, indica al responsabile della manutenzione quanto può riporre fiducia in una determinata apparecchiatura.
L'affidabilità si misura con una serie di strumenti. I principali sono:
- FMEA(Failure Modes and Effects Analysis), che identifica i danni alle apparecchiature prima che si verifichino, quali sono le cause e le conseguenze. Classifica i guasti calcolando il numero di priorità di rischio (RPN), ponderando così la natura del guasto, il modo in cui si è verificato e la sua gravità.
- FTA(Fault Tree Analysis), l’albero dei guasti, un approccio organizzato e logico per mettere in relazione i guasti e le loro cause. Ricostruendo inversamente il processo che ha portato al problema, l'analisi dell'albero dei guasti permette al manager di scoprire le radici del guasto.
Ciò premesso, quando si parla di affidabilità degli asset, l’indicatore più famoso è il MTBF, il tempo medio tra i guasti. Si tratta di uno degli indicatori più importanti dell'intero settore della manutenzione perché misura il tempo medio di funzionamento delle apparecchiature riparabili tra un guasto e l'altro, escludendo i tempi di inattività programmati. Più lungo è il tempo medio di buon funzionamento, più affidabile è il sistema.
Analisi di disponibilità (Availability)
A differenza dell'affidabilità e della manutenibilità, la disponibilità è un concetto che riguarda il passato e si riferisce al periodo di tempo in cui un impianto è stato disponibile per svolgere le sue funzioni specifiche. In altre parole, la disponibilità rappresenta la capacità di un asset di svolgere il ruolo designato per un certo periodo di tempo.
Per calcolare la disponibilità operativa nel settore manifatturiero, si confrontano le ore macchina disponibili con il numero di ore di lavoro pianificate. Per le ore di lavoro pianificate, si sommano i tempi di attività e i tempi di inattività.
I due indicatori su cui si basa il calcolo sono MTBF e MTTR, o Mean Time To Repair, che analizza il tempo medio necessario al team per riparare la macchina.
Per stimare questo tempo, si sommano le ore di riparazione e si divide per il numero di interventi effettuati.
Analisi di manutenibilità (Maintainability)
Un altro indicatore è la manutenibilità, elemento che si concentra sulla facilità di riparazione di un bene per riportarlo al suo normale funzionamento dopo un guasto.
La manutenibilità si focalizza pertanto sull'eliminazione di ostacoli e di difficoltà nelle azioni dei tecnici e sul mantenimento delle buone prestazioni della macchina. Ne consegue che quanto più è difficile riparare un'apparecchiatura e riportarla al suo corretto stato operativo, tanto più bassa sarà anche la manutenibilità.
Ciò premesso, una condizione di bassa manutenibilità comporta un aumento dei costi di manutenzione, una riduzione della produttività aziendale e un aumento del lavoro per il team di manutenzione e affidabilità.
Nell’ipotesi di un MTTR particolarmente basso, la manutenibilità è alta, indicando che l’impianto impiega poco tempo per tornare al suo stato produttivo. Migliorare l'MTTR significa dunque migliorare sia la disponibilità che la manutenibilità di qualsiasi apparecchiatura.

In sintesi, l'analisi della manutenibilità spesso richiede una valutazione umana per considerare gli aspetti critici per il lavoro del team di manutenzione, come ad esempio concerne l’accesso del personale ai punti di riparazione e ispezione, la necessità di spostare le apparecchiature in una nuova location, le condizioni di lavoro e la sicurezza del personale durante le riparazioni e le ispezioni e la distribuzione ottimizzata delle attrezzature per eliminare la mancanza di produttività.
Analisi di sicurezza (Safety)
Ai termini di cui sopra se ne accompagna un altro, l’ultimo (ma non certo in ordine di importanza): la sicurezza.
La sicurezza (safety) di un impianto o di un processo è definibile come la probabilità di accadimento di un evento potenzialmente pericoloso per l’ambiente o per le persone. Anche in questo caso, sussistono differenti tecniche che possono aiutare l’organizzazione a effettuare l’analisi dei rischi, allo scopo di valutarne e mitigarne il più possibile gli effetti.
Tra le principali:
- HAZOP (Hazard and operability analysis): basata sul lavoro di gruppo, ha come obiettivo quello di individuare i pericoli esistenti in un determinato processo produttivo o manutentivo;
- LOPA (Layer of protection analysis): consente di verificare l’efficacia delle misure di sicurezza adottate all’interno di un’azienda, con lo scopo di comprendere quanti e quali sono i diversi livelli (layers) necessari a ridurre il rischio generato da un guasto o da un’anomalia;
- PHA (Process Hazard Analysis): permette di individuare quali sono rischi pericoli legati ad un processo di produzione industriale, a partire dalle potenziali cause e conseguenze di guasti, eventi ambientali o errori umani.
Evidentemente, l’analisi dei rischi mediante le tecniche di cui sopra non potrà che essere integrata dall’osservazione delle prescrizioni di legge in termini di sicurezza.