- Pubblicato il 26 ott 2023
- Ultima modifica 29 feb 2024
- 4 min
FMEA, ovvero in che modo i guasti migliorano l'ingegneria della manutenzione
Gli ingegneri dedicano molto tempo per evitare i guasti degli asset, ma imparare da questi dagli stessi quando si verificano è fondamentale per migliorare le strategie di manutenzione di impianti e macchinari.
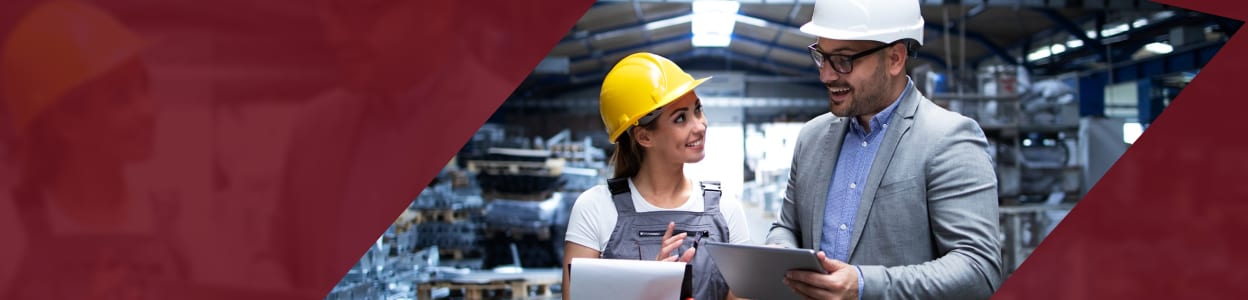
Nessuno vuole affrontare un guasto, maanche se proprio dai guasti è possibile imparare eottenere un patrimonio informativomoltissime informazioni utili utileper evitare che le interruzioni nelle operatività degli asset accadano di nuovo e per contribuire amigliorare l’efficienza del facility management.
Per far ciò, come vedremo nella seconda parte di questo approfondimento, è innanzitutto necessario stabilire ciò che ha causato il disservizio: un approccio strutturato come il Failure Modes and Effects Analysis (FMEA) è certamente il più raccomandabile poiché, se usato correttamente, consente di individuare potenziali modalità di guasto, arrivare alla causa principale e identificare azioni per eliminare le cause dei malfunzionamenti.
Peraltro, l’uso di un’analisi FMEA non richiede nemmeno unsoftware particolarmente sofisticatio: in molti casi potrebbe essere sufficiente un solo foglio di calcolo Excel in cui elencare i guasti e ciò che potrebbe averli causati. Nel caso in cui si dovesse notare qualcosa che accade regolarmente, sarà evidentemente alloranecessario agire con tempestività.
In aggiunta a ciò, vale sempre la pena dedicare del tempo a esaminare come attualmente vengono rilevati i guasti per assicurarsi di ottenere un quadro preciso di ciò che sta accadendo: organizzare periodiche sessioni di brainstorming con gli operatori interessati da tali attività può permettere di individuare le cause principali.
L’importanza dell’investigazione come punto di partenza nell’FMEA
Fatte salve le premesse di cui sopra, e rammentata l’importanza di un approccio FMEA, quando accade un guasto è molto importante rimanere calmi e adottare un approccio analitico. Prendersi del tempo per riflettere durante la risposta a un guasto è essenziale, considerando sempre tutte le possibilità nella consapevolezza che spesso i dati sono scarsi: nei sistemi manuali - e la maggior parte delle aziende funziona ancora con essi, anziché raccogliere dati dai loro sistemi integrati - spesso le informazioni sono rilevate da un operatore che potrebbe non essere in grado di rilevare con precisione elementi utili per attribuire correttamente le determinanti di un guasto.
Ecco dunque che è fondamentale come per gli ingegneri di manutenzione nel settore manifatturiero debbano rivedere di frequente rivedere l'approccio adottato: è sempre meglio non trarre conclusioni affrettate, ma seguire le prove fino all’origine del guasto.
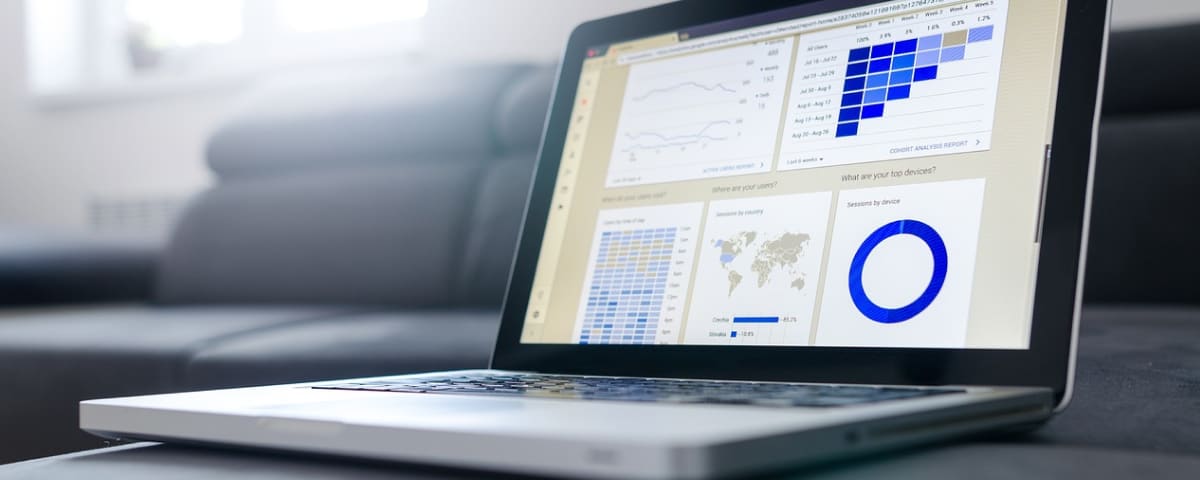
Cambiare la cultura della manutenzione
L’approccio fondamentale per la corretta valorizzazione informativa dei guasti è pertanto quello legato all’attento esame di tutte le informazioni disponibili sull’asset che è stato interessato dal malfunzionamento, compresi i registri di manutenzione che possono fornire informazioni essenziali su ciò che è andato storto.
Fornire un cruscotto che operatori e ingegneri possano utilizzare aiuterà infatti non solo a evitare nuovi guasti, ma contribuirà anche a promuovere un cambiamento culturale positivo nell'organizzazione produttiva.
Ma una volta conosciuta la causa, come si può garantire che tutti coloro che necessitano di queste informazioni ricevano il messaggio per evitare un evento guasto ripetuto?
Purtroppo, l’evidenza quotidiana ci conduce a ritenere che buona parte delle organizzazioni non siano sufficientemente abili nel raccogliere e sfruttare le loro proprie conoscenze collettive e condividerle condividendole internamente. Parte del problema è pertanto che la comunità operativa non sia ben collegata dagli OEM (i produttori di attrezzature originali): la maggior parte delle persone che progettano l'attrezzatura non la utilizzano e la maggior parte degli operatori non la progetta.
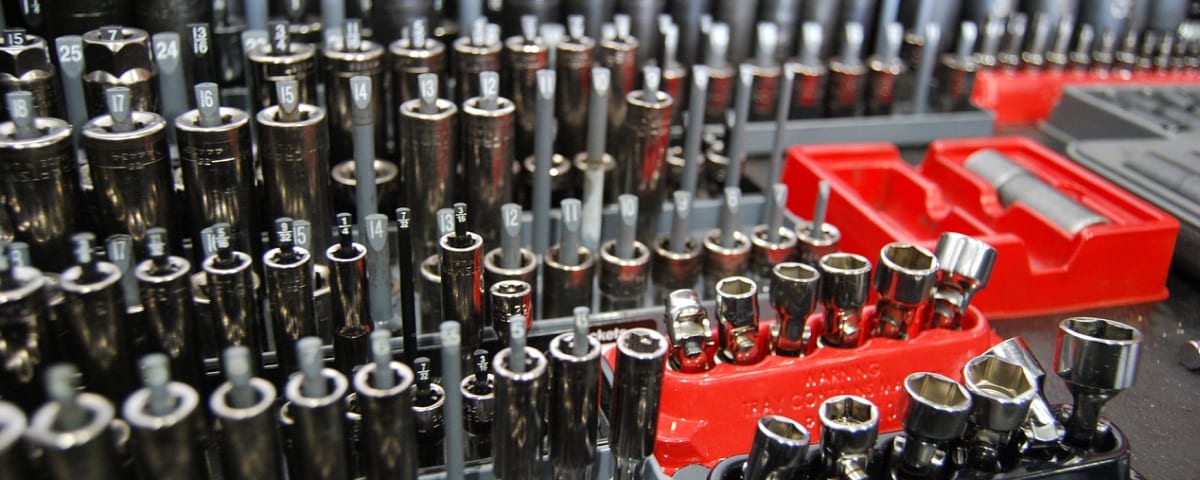
FMEA: come individuare la causa principale dei guasti
Analizzare i guasti in modo che non si ripetano porterà a una maggiore disponibilità e produttività. Tuttavia, occorrono tempo e un approccio rigoroso che vadano ad indagare la causa principale del problema. Se gli ingegneri di manutenzione coinvolgono operatori e responsabili nel processo, possono beneficiare del miglioramento del morale e di una cultura migliore per l'intera organizzazione.
In questo ambito, un metodo analitico per individuare le cause del guasto e sfruttare le informazioni che ne derivano per il miglioramento dell’ingegneria della manutenzione è quello sequenziale, strutturato in 7 azioni consequenziali.
Identificare il problema
La prima fase consiste nel comprendere che cosa è accaduto all’impianto o all’apparecchiatura attraverso il rilievo di informazioni chiare e inequivocabili.
Raccolta delle informazioni
Identificato il problema, si passa alla rilevazione delle informazioni che descrivano in maniera dettagliata i sintomi dell’irregolare funzionamento dell’asset. È utile verificare anche la storia dei guasti, poiché possibile fonte di informazioni sul guasto attuale. Gli elementi più importanti devono essere riportati in schede Event and Casual Factors.
Valutazione della qualità delle informazioni
Le informazioni così ottenute devono essere poi valutate in termini quantitativi e qualitativi, esaminando lo storico dei guasti e consultando i manuali dell’impianto e ogni altro supporto coerente.
Analisi delle informazioni
La quarta azione è quella dell’analisi delle informazioni, un metodo di diagnosi analitico che possa fornire risposte alle seguenti domande:
- che cosa è accaduto e che cosa sarebbe dovuto invece succedere e non si è realizzato per garantire il buon funzionamento;
- dove è accaduto il guasto di quel componente e non di altri componenti in condizioni identiche o equivalenti;
- quando si è manifestato l’evento di guasto e perché non si è manifestato in altre occasioni simili;
- come si realizza l’evento di guasto e come invece non si realizza (individuazione di una sequenza di cause-effetto che conducono alla situazione di guasto);
- chi stava lavorando sulla macchina nel momento in cui si è verificato il guasto e in che modo la sua attività potrebbe aver differito rispetto alle procedure operative, contribuendo ad alimentare una condizione di guasto;
- perché il guasto si realizza con specifiche modalità mentre non si rileva in altri casi, condizioni o iter operativi differenti.
Proposta delle soluzioni
Con le informazioni ottenute nelle fasi precedenti si ipotizzano diverse soluzioni, si predispongono prove per verificare quale soluzione permetta di individuare il guasto e riparare la parte danneggiata e si considera altresì il costo della riparazione.
Verifica delle soluzioni
Si procede alla verifica delle soluzioni con la sperimentazione per comprendere se l’analisi sia stata o meno corretta.
Realizzazione della riparazione
L’ultima fase è infine rappresentata dalla riparazione, con l’operatore che – a intervento eseguito – procede con il completamento della reportistica.