- Pubblicato il 28 mag 2024
- Ultima modifica 28 mag 2024
- 6 min
MRP: significato e differenze con ERP
Nonostante l’introduzione del sistema ERP, il Material Requirements Planning rappresenta ancora oggi un perno di valutazione fondamentale per le imprese produttive.
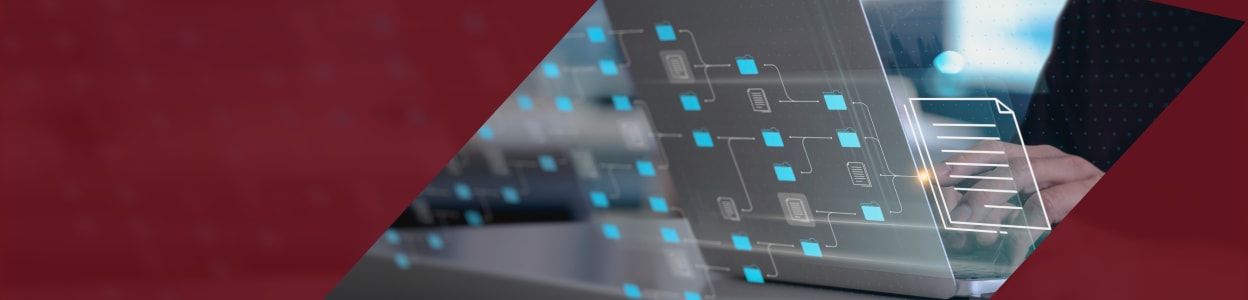
Il termine Material Requirements Planning (MRP) si riferisce a un sistema per il calcolo dei componenti necessari per la realizzazione di un prodotto. Composto da alcune fasi consequenziali personalizzabili, è dunque un approccio molto importante per le organizzazioni produttive.
Proprio per questo motivo, nelle prossime righe cercheremo di comprendere quali siano le caratteristiche del MRP, come funziona e perché è così importante per la sostenibilità delle attività di impresa.
Perché il MRP è così importante?
Cominciamo proprio da questo punto. Per quale motivo il Material Requirements Planning è così importante?
Il MRP, di norma utilizzato mediante l’ausilio di software ad alta specializzazione, aiuta l’organizzazione a garantire che all’interno del proprio magazzino sia disponibile l’inventario sufficiente per la corretta esecuzione del processo produttivo, rendendolo disponibile esattamente quando necessario e al minor costo possibile.
Analizzare il MRP significa dunque migliorare l’efficienza dell’azienda, la sua flessibilità e la redditività delle operazioni di produzione, riducendo al minimo i costi legati all’acquisizione del materiale e della manodopera.
Non solo: il MRP aiuta anche i produttori a rispondere più rapidamente all’incremento della domanda dei loro prodotti ed evitare possibili ritardi nella produzione e nelle scorte di inventario che possono causare la perdita dei clienti o la loro fidelizzazione.
Come funziona il Material Requirements Planning?
Il Material Requirements Planning usa un set informativo (di norma, i dati di inventario, il programma di produzione e la bill of materials) per calcolare quali siano i componenti richiesti per il processo di produzione e quando saranno necessari nelle varie fasi della fabbricazione.
Il MRP è dunque utilizzato nella maggior parte delle aziende per tracciare e gestire in modo integrato tutte queste variabili, arrivando così a stimare il numero e la qualità delle materie prime e dei componenti necessari entro le date specificate nel programma di produzione.
Insomma, in altri termini, il MRP è un sistema di gestione e di controllo dell’inventario utile a ordinare e monitorare gli articoli necessari per realizzare un prodotto.
In questo contesto, anche il tempo di consegna diviene un altro concetto chiave in MRP. Sebbene si debbano tenere in considerazione diverse tipologie di tempistiche, quelli più rilevanti rimangono i tempi di consegna dei materiali (cioè, il tempo necessario per ordinarli e riceverli) e di consegna della produzione (il tempo necessario per produrre e spedire il prodotto dopo che tutti i materiali sono pronti per l’uso). Tra le altre metriche, vi è poi anche il tempo di consegna del cliente, che indica il tempo che intercorre tra l’ordine del cliente e la consegna finale. Si consideri che il MRP calcola molti di questi tempi di consegna, ma alcuni rimangono scelti liberamente dai responsabili delle operazioni e inseriti manualmente nel sistema.
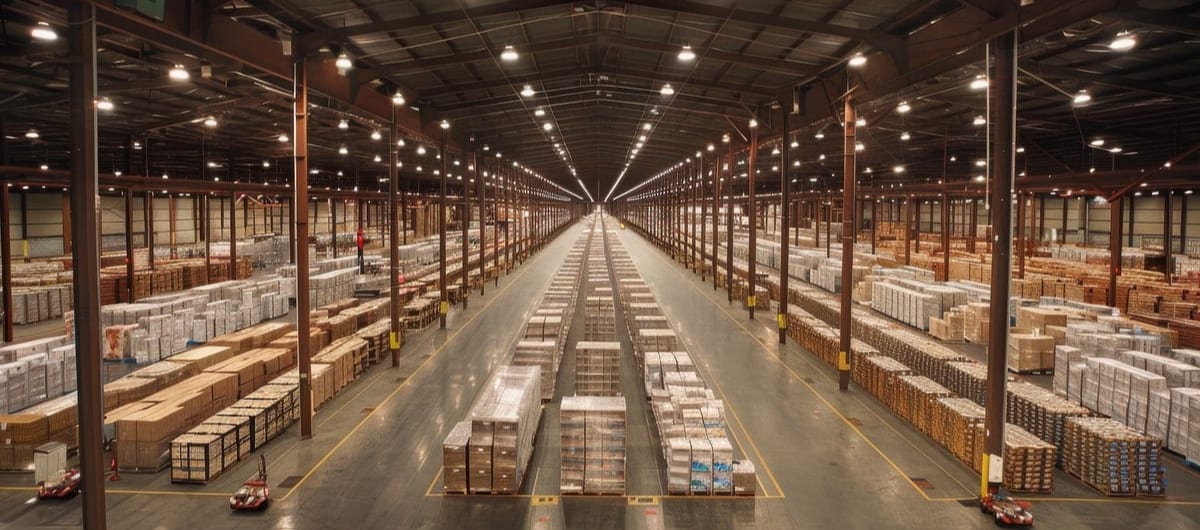
Pro e contro del MRP
A questo punto, compreso che cosa sia il MRP e per quali motivi è importante, possiamo fare un piccolo passo in avanti e domandarci quali siano i pro e i contro di questo sistema.
Partendo dall’obiettivo principale, che è quello di assicurarsi che i materiali e i componenti siano sempre disponibili quando necessario lungo il processo di produzione e che la produzione avvenga nei tempi previsti, i principali vantaggi del MRP sono:
- riduzione dei tempi di consegna dei prodotti ai clienti con miglioramento della loro soddisfazione
- riduzione dei costi di inventario e logistici
- efficace gestione dell’inventario e ottimizzazione dello stesso (si acquisiscono le quantità e il tipo di inventario ottimale per i propri obiettivi, contenendo al minimo le scorte e il loro impatto negativo in azienda)
- miglioramento dell’efficienza produttiva mediante una più accurata pianificazione e programmazione della produzione per ottimizzare l’uso di manodopera e attrezzature
- miglioramento della produttività del lavoro
- maggiore competitività a livello di prezzi
Vi sono tuttavia anche alcuni svantaggi dell’uso del MRP o, almeno, alcuni punti di attenzione. Tra i più noti:
- sovrapposizioni nel magazzino: anche se il MRP è esplicitamente progettato per garantire livelli adeguati di magazzino nei tempi richiesti, è pur sempre possibile che l’azienda sia tentata di detenere più inventario del necessario, aumentandone così i costi. Un sistema MRP tende inoltre ad anticipare prima la carenza, che può portare a sopravvalutare le dimensioni dei lotti nell’inventario e i relativi tempi di consegna, soprattutto nei primi giorni di implementazione del sistema;
- ridotta flessibilità: il sistema MRP è un po' rigido e semplicistico nel modo in cui tiene conto dei tempi di consegna o dei dettagli che influenzano il programma di produzione, come ad esempio avviene per l’efficienza degli operati o dei problemi che possono ritardare la consegna dei materiali;
- necessità di avere dati accurati: il MRP dipende fortemente dalla disponibilità di accesso a informazioni accurate sugli input chiave, come la domanda, l’inventario e la produzione. Pertanto, se i dati di partenza non sono accurati, gli errori possono finire per essere sempre più rilevanti nelle fasi successive.
Ecco dunque che, per ovviare a queste carenze, sono sempre di più le aziende che preferiscono utilizzare un software avanzato di pianificazione, che usa raffinati sistemi algoritmici per fornire stime ancora più accurate dei tempi di consegna. Contrariamente alla maggior parte dei sistemi MRP, infatti, il software APS tiene conto della capacità di produzione, elemento che può impattare in modo significativo sulla disponibilità dei materiali.
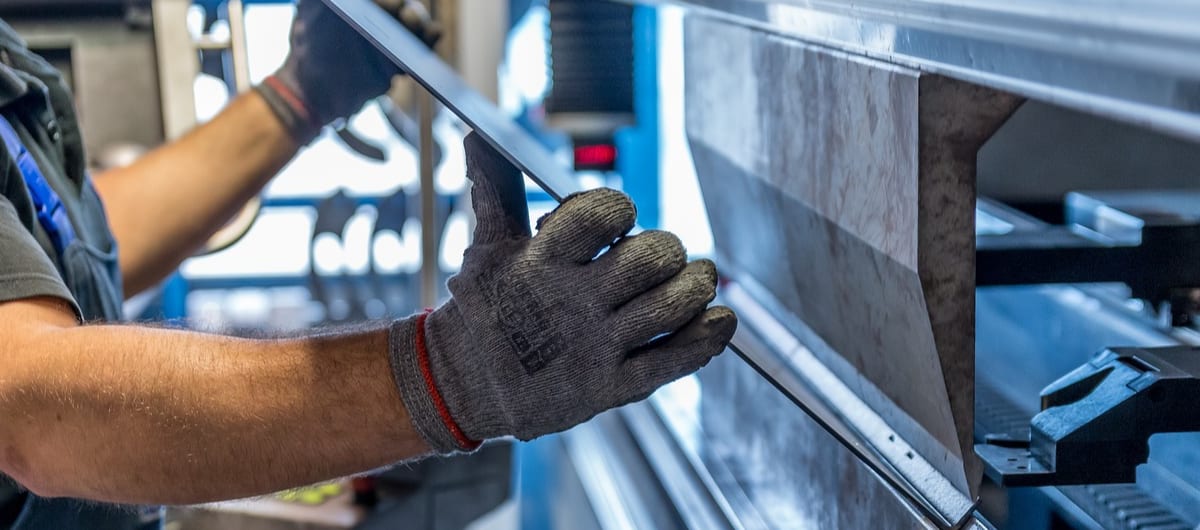
MRP o ERP: quali sono le differenze?
Nel 1983 l’ingegnere IBM Oliver Wight sviluppò un’evoluzione di MRP chiamata MRP II, con cui ampliava il processo di pianificazione, includendo altre risorse nell’azienda, come i dati finanziari, le stime necessarie per la progettazione del prodotto, la gestione dei costi, la pianificazione delle vendite e altro ancora.
Nel 1990, poi, la società di analisi Gartner coniò un ulteriore termine per la pianificazione delle risorse aziendali, ERP (Enterprise Resource Planning) LINK NON ANCORA LIVE, a indicare un tipo ancora più amplio e generalizzato di MRP II, in grado di tenere conto di altre importanti funzioni dell’azienda come la contabilità, le risorse umane o la gestione della catena di approvvigionamento, attraverso un unico database centralizzato.
In tal senso, dunque, ERP si pone come un’ulteriore evoluzione di MRP. Come tale, in virtù di una maggiore efficienza e puntualità, il sistema si estese ad altri settori come i servizi, le banche e la vendita al dettaglio, che non necessitavano delle componenti tipiche del sistema MRP, il quale però rimane ancora una parte importante del software ERP dei produttori.
Insomma, anche alla luce delle evoluzioni in ERP, MRP rimane un elemento essenziale per comprendere l’efficienza, l’efficacia e la redditività delle operazioni di produzioni in un’impresa.
D’altronde, senza disporre delle giuste materie prime e dei componenti fondamentali a portata di mano, i produttori non possono certamente ottimizzare il proprio processo di realizzazione dei prodotti e non saranno in grado di rispondere prontamente alle fluttuazioni della domanda, adeguandone la produzione.