- Pubblicato il 7 mar 2024
- Ultima modifica 10 giu 2024
- 5 min
RCA: usare la Root Cause Analysis per trovare le cause dei guasti e i loro effetti
La RCA è tra i metodi più conosciuti e usati per trovare le cause dei guasti e i loro effetti e prolungare la vita degli impianti e delle apparecchiature: ma in cosa consiste e come funziona?
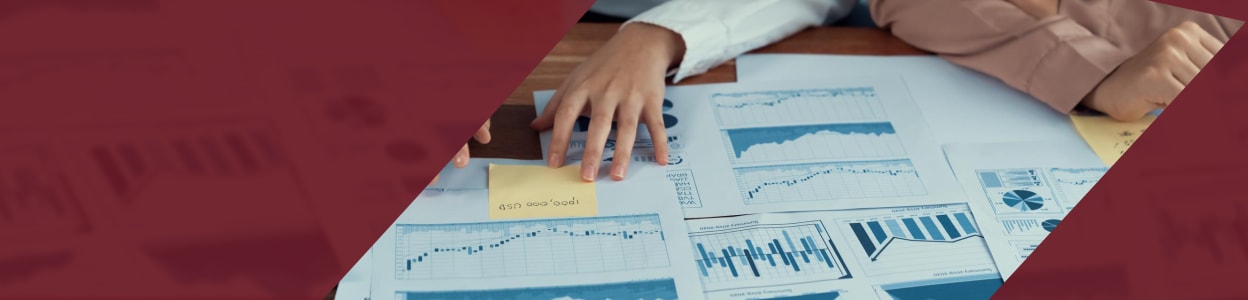
Tra i metodi conosciuti e usati di analisi dei problemi, la Root Cause Analysis (o analisi delle cause radice) è sicuramente uno dei più diffusi: l’approccio punta a individuare la causa principale del problema, ovvero un fattore che ha causato una non conformità e che dovrebbe essere eliminato in modo permanente attraverso il miglioramento dei processi.
La causa centrale è dunque la determinante dei guasti, l’origine che pone in moto l'intera reazione di causa-effetto che alla fine porta all’emersione del problema: scoprirla significa prolungare il ciclo di vita degli impianti e delle apparecchiature, implementando le soluzioni migliori.
Tutto ciò premesso, sarebbe più corretto definire la Root Cause Analytics non certo un unico tipo di approccio, ma un insieme di approcci, strumenti e tecniche che sono coerentemente usati per scoprire le cause dei problemi e, in particolar modo, la determinante principale.
Di fatti, alcuni approcci RCA sono più orientati all'identificazione delle vere cause profonde rispetto ad altri, mentre altri sono tecniche più generali orientati alla risoluzione dei problemi. Altri ancora sono invece in grado di offrire semplicemente un supporto all'attività principale dell'analisi delle cause profonde.
È inoltre corretto ricordare come la RCA sia riconducibile al campo più ampio della gestione della qualità totale, o Total Quality Management (TQM), un’ottica gestionale al cui interno è possibile trovare proprio, tra gli altri, sia il problem solving che la Root Cause Analysis.
Ancora, la RCA è altresì inquadrabile all’interno di un processo più generale di risoluzione dei problemi in termini di miglioramento continuo: proprio per questo motivo la RCA costituisce uno degli elementi fondamentali degli sforzi di miglioramento continuo di un'organizzazione ed è importante notare che l'analisi con la RCA di per sé non produrrà alcun risultato ma dovrà essere inserita in un più ampio sforzo di risoluzione dei problemi per il miglioramento della qualità.
Ma allora perché viene effettuata la RCA? Come si conduce questo tipo di analisi?
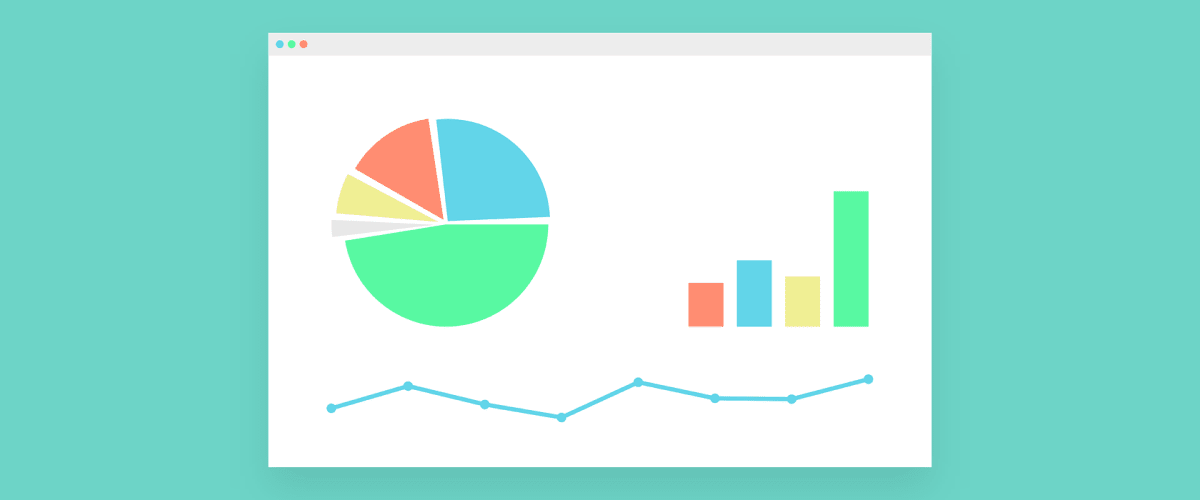
Gli approcci alla RCA
Come anticipavamo, non esiste un unico approccio alla RCA, bensì un insieme di tecniche integrate che consentono di effettuare in modo specifico e accorto la Root Cause Analysis.
Tra le principali rileviamo:
- Analisi degli eventi e dei fattori causali: utilizzato prevalentemente per i problemi più gravi e singoli eventi, come ad esempio il definitivo KO di un intero impianto, questo approccio usufruisce delle prove raccolte in modo rapido e metodico al fine di stabilire una cronologia delle attività che hanno portato all'incidente. Una volta stabilita la cronologia si può procedere con l’identificazione dei fattori che hanno causato il problema o hanno comunque contribuito in modo più o meno diretto.
- Analisi dei cambiamenti: è un approccio applicabile soprattutto in quelle situazioni in cui le prestazioni di un sistema hanno subito un cambiamento significativo. Con questo approccio si potranno analizzare le modifiche apportate a persone, attrezzature, informazioni e altro ancora, che possono aver contribuito al cambiamento delle prestazioni.
- Analisi delle barriere: la tecnica analitica si concentra in questo caso su quali controlli siano presenti nel processo per prevenire o per rilevare un problema e quali potrebbero aver contribuito all’emersione del problema.
- Analisi dell'albero dei rischi: si tratta di un approccio piuttosto utilizzato, che utilizza l’osservazione di un diagramma ad albero per esaminare cosa si è verificato e perché potrebbe essersi verificato.
- Risoluzione dei problemi e processo decisionale di Kepner-Tregoe: è un modello strutturato in quattro distinte fasi per la risoluzione dei problemi (analisi della situazione, analisi del problema, analisi della soluzione, analisi del problema potenziale).
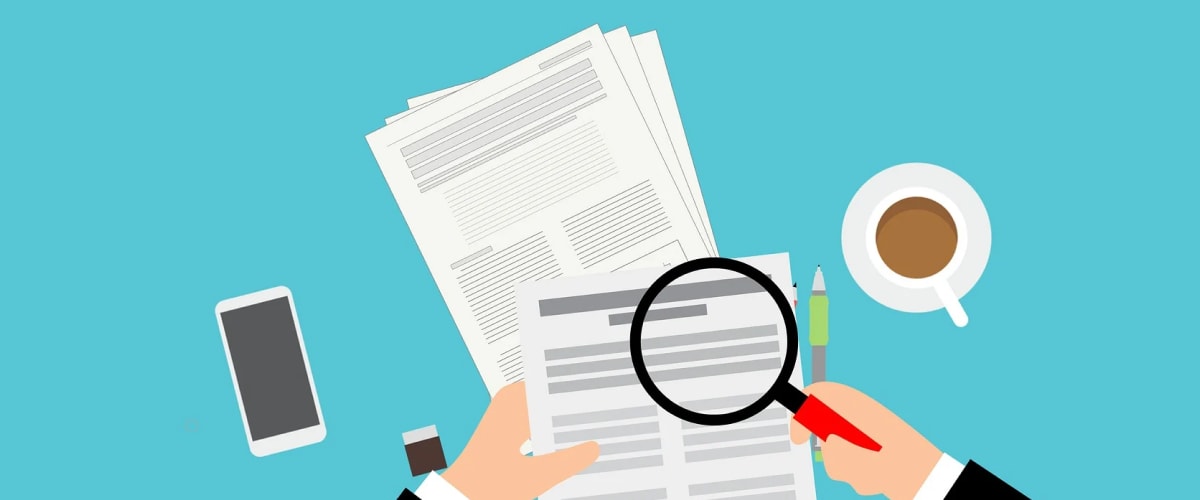
Come si effettua la Root Cause Analysis
Quando ci si avvicina a uno degli approcci RCA è importante rammentare che anche se molti strumenti di analisi delle cause profonde possano essere utilizzati da una sola persona, il risultato è generalmente migliore quando un gruppo di persone lavora insieme per individuare le cause del problema in un quadro MRO.
Ecco perché gli approcci RCA sono generalmente inquadrati a livello di team, di norma a diretto riporto del top management.
Un esempio di progettazione di un'analisi delle cause profonde in un'organizzazione potrebbe seguire le seguenti fasi:
- Formazione del team che si occuperà di condurre l'analisi RCA. I membri del team sono selezionati dal processo aziendale che presenta il problema e possono essere coadiuvati da un manager di linea con l'autorità decisionale di implementare le soluzioni, da un cliente interno del processo con problemi, da un esperto di miglioramento della qualità nel caso in cui gli altri membri del team abbiano poca esperienza in questo tipo di lavoro.
- Analisi vera e propria. Il processo ha una durata variabile ma raramente si conclude entro poche settimane. Durante questa fase, si pone la stessa enfasi sulla definizione e sulla comprensione del problema, sul brainstorming delle possibili cause, sull'analisi delle cause e degli effetti e sull'elaborazione di una soluzione al problema. Durante il periodo di analisi, il team si riunisce almeno settimanalmente, a volte due o tre volte alla settimana, con riunioni brevi e ordine del giorno con ampi margini di libertà. A una persona del team viene assegnato il ruolo di assicurare l'avanzamento dell'analisi, oppure i compiti vengono assegnati a vari membri del team.
- Implementazione della soluzione. Una volta che il team ha individuato e scelto la soluzione, si procederà alla fase di implementazione, seguita da un costante monitoraggio e da un confronto dei risultati ottenuti con quanto auspicato.
I 5 Metodi più diffusi per la RCA
Come abbiamo più volte sottolineato nelle scorse righe, quando si parla di Root Cause Analysis sarebbe più corretto riferirsi alla possibilità di ricorrere alla fruizione di più metodi, ben diversi tra di loro, ma accomunati dalla possibilità di identificare i fattori che possono contribuire al verificarsi di un guasto.
5 Why’s Analysis (o analisi dei 5 perché)
Tra i metodi più diffusi per la RCA troviamo ad esempio la 5 Why’s Analysis, o analisi dei 5 perché, forse il modo più semplice e usato per l’analisi delle cause radice. Sorto in seno al Toyota Production System negli anni ’70, è un metodo che consiste nell’individuare e rispondere a una serie di domande che bisogna porsi per circoscrivere il problema e indagarne in modo approfondito la causa scatenante.
L’idea alla base di questo metodo di indagine delle cause principali è che la risposta a ogni perché diventi la base della domanda successiva.
Diagramma di Pareto
Un altro modello RCA è quello del diagramma di Pareto, che fonda la propria base sul fatto che l’80% dei problemi sia determinato dal 20% delle cause critiche: si costruisce così un grafico a barre combinato con un grafico a linea, con le barre che mostreranno la frequenza dell’evento e le linee che determineranno il costo cumulativo o in percentuale.
Diagramma di Ishikawa
Un altro metodo molto utilizzato è il diagramma causa – effetto, conosciuto anche come diagramma di Fishbone o diagramma di Ishikawa. Come altri, anche questo metodo permette di mappare visivamente le cause e gli effetti che un guasto ha sul processo, seguendone poi le diramazioni sulla base di ogni categoria individuata.
Diagramma a dispersione
Ancora, possiamo individuare certamente il diagramma a dispersione, che aiuta a scoprire diverse relazioni tra variabili, così come la Fault Tree Analysis, l’analisi dell’albero dei guasti, che mostra visivamente quali siano gli effetti di un guasto sul nostro processo.
Analisi dei guasti e degli effetti (FMEA)
Un altro metodo pratico – l’ultimo che individuiamo in questa breve sintesi – è quello dell’analisi dei guasti e degli effetti (FMEA), spesso usato durante la fase di progettazione del processo per disporre di una visione più ampia di potenziali difetti o di possibili guasti.