- Pubblicato il 3 giu 2024
- Ultima modifica 3 giu 2024
- 5 min
DDMRP: cos'è e come funziona
Il DDMRP (Demand Driven Material Requirements Planning) rappresenta un’interessante evoluzione del MRP: ecco come funziona e quali sono i vantaggi per le moderne organizzazioni.
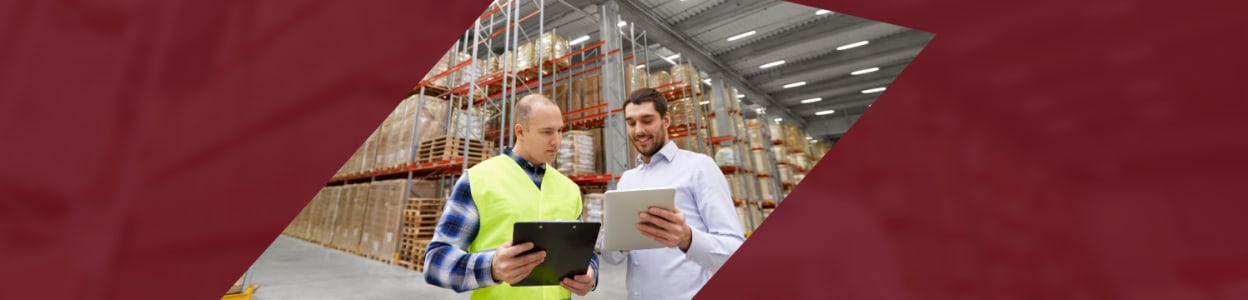
DDMRP (Demand Driven Material Requirements Planning) è una recente versione del MRP in grado di combinare tutte le qualità del sistema originario, con nuove tecnologie che possono rispondere in modo ancora più competitivo alle sfide contemporanee.
Per cercare di comprendere più nel dettaglio quali siano i vantaggi del DDMRP, giova tuttavia compiere una piccola premessa e ricostruire, in sintesi, quali siano le caratteristiche del MRP, il Material Requirements Planning, dal quale la nostra presente guida trae origine.
Cos’è il MRP e come si è arrivati al DDMRP
Il MRP è conosciuto per essere stato la base dei sistemi di produzione per più di 50 anni. Il suo ambizioso obiettivo è quello di determinare quali componenti e materiali ordinare, in quali quantità e con che tempistiche. In aggiunta a ciò, individua anche quando le attività di produzione devono iniziale, per poter completare i lavori entro la data prevista.
Per riuscire a fornire una stima puntuale, MRP si basa su previsioni della domanda basate sulle informazioni pregresse.
Per quanto utile e in grado di costituire la base di numerosi software che hanno trovato ampio spazio nelle aziende che si occupano di attività produttive, MRP negli anni ha finito con l’essere superato da altri sistemi, diventando una mera funzione standard di un sistema ERP moderno.
Negli anni, poi, ci si è resi conto che il sistema MRP non era più in grado di rispondere efficacemente al nuovo contesto, più complesso e incerto, dell’approvvigionamento, le cui catene prevedono tempi di consegna a volte sempre più lunghi, poiché le materie prime e i componenti arrivano da ogni parte del mondo. Molte aziende hanno dunque riferito di aver superato autonomamente il sistema ERP, poiché temono di non potersi approvvigionare nei tempi stimati attraverso tale approccio preferendo, dunque, acquisire scorte magari eccessive.
Si giunge così a sperimentare con successo nuove iterazioni di MRP tra cui, appunto, il protagonista del nostro odierno approfondimento, il DDMRP (Demand Driven Material Requirements Planning). Sebbene relativamente nuovo, il DDMRP ha già dimostrato di essere utile per prendere in prestito e combinare tutti i migliori elementi dei più collaudati principi di produzione.
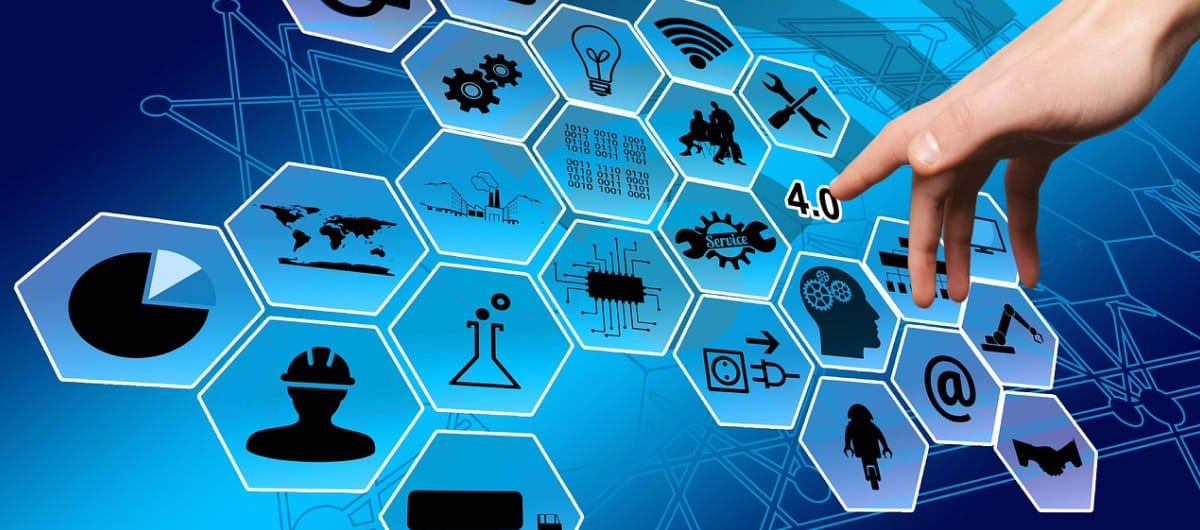
I componenti del DDMRP
Il DDMRP ha strutturalmente cinque step sequenziali. I primi tre definiscono la configurazione iniziale e in evoluzione di un modello di pianificazione dei requisiti dei materiali basato sulla domanda, mentre gli ultimi due definiscono il funzionamento quotidiano del metodo:
- Posizionare strategicamente l’inventario: il primo passo è quello di identificare i punti di disaccoppiamento nella rete della catena di approvvigionamento, in cui inserire un buffer da monitorare e reintegrare;
- Identificare le qualità del buffer: per ognuno dei punti di disaccoppiamento sopra individuati, occorrerà poi identificare le dimensioni del buffer (quantità minima e massima e punto di riordino) e la quantità del riordino;
- Regolare il buffer: il terzo step è determinato dalla regolazione dei livelli di buffer sulla base di parametri operativi variabili o eventi futuri pianificati;
- Pianificare la domanda: si giunge così al quarto step, in cui vengono generati gli ordini di fornitura nel momento in cui essi vengono richiesti. Gli ordini di fornitura includono sia gli ordini di produzione che quelli di acquisto o di trasferimento delle scorte;
- Dare seguito agli ordini:infine, si procede con l’esecuzione degli ordini di fornitura, come previsto dalle linee guida del DDMRP.
Differenze tra MRP e DDMRP
Ora, per comprendere a pieno la differenza tra MRP e DDMRP, bisogna comprendere la diversità tra un sistema push e uno pull. MRP è infatti tipicamente un sistema push: sulla base delle informazioni pregresse, vengono stimate delle previsioni che anticipino la domanda futura.
Il sistema DDMRP è invece un sistema pull, che prevede un disaccoppiamento della domanda e dell’offerta così da evitare il c.d. effetto bullwhip, ovvero le piccole fluttuazioni della domanda a livello di vendita al dettaglio che possono a loro volta causare fluttuazioni progressivamente maggiori della domanda a livello di grossista, distributore e produttore. Il perno del sistema è la predisposizione dei buffer, che possono garantire il mantenimento della quantità corretta di stock, coprendo l’uso medio di un componente e potendosi regolare per coprire i picchi di domanda.
Insomma, invece di dipendere dall’accuratezza delle previsioni e accumulare delle scorte “tampone” contro le fluttuazioni tipiche della domanda e dell’offerta, il DDMRP tiene traccia dell’uso effettivo e gestisce il riapprovvigionamento mediante un sistema visivo. Ne deriva che lo stock tampone è utilizzato solamente per assicurare la disponibilità effettiva dei componenti chiave, ritenuti di importanza strategica.
Così facendo, nell’ipotesi di un corretto uso del sistema, si riduce il livello generale dello stock e si contiene il rischio di carenze di componenti.
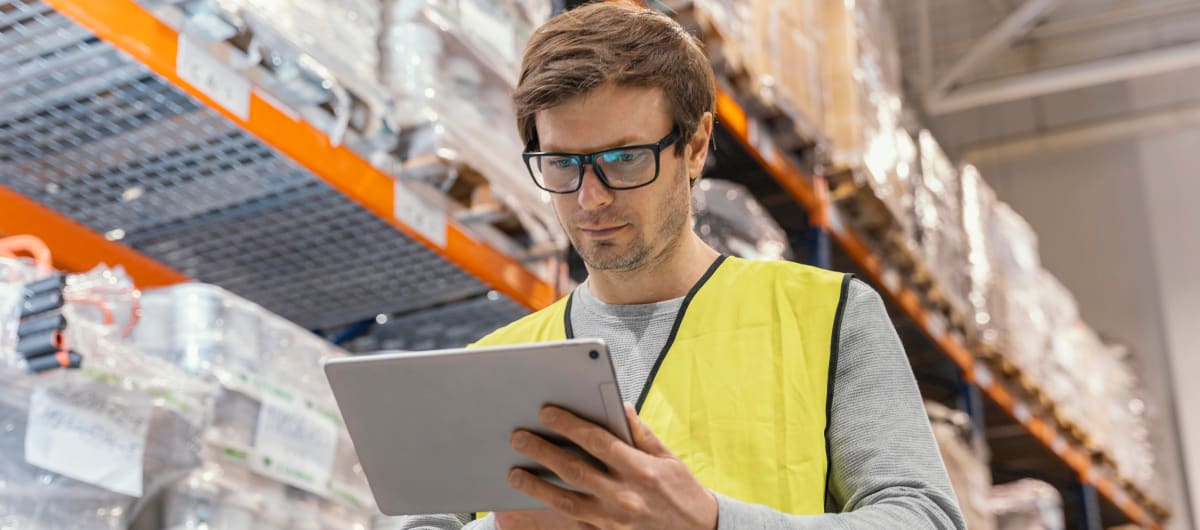
DDMRP e l’approccio P-P-P
Un metodo ancora più semplice e diffuso per illustrare quale sia il funzionamento del DDMRP è quello P-P-P, ovvero Positionà Protectà Pull:
- Position: si esaminano le distinte base per individuare i componenti e i materiali strategici nei vari punti critici presenti all’interno delle strutture dell’organizzazione, che diverranno poi oggetto di massima attenzione;
- Protect: la disponibilità degli articoli ritenuti critici viene assicurata anche affidando al magazzino la funzione di tampone. Contrariamente a quanto avviene nel metodo MRP, in cui tale buffer viene costituito nella pianificazione iniziale, nel DDMRP invece si procede a riapprovvigionare dinamicamente in base alle esigenze;
- Pull: lo stock tampone è gestito mediante una tecnica pull che monitora continuamente i livelli di inventario e attiva segnali visivi per mantenere il buffer entro un range determinato.
Con questa struttura, il DDMRP richiede meno stock, considerato che il magazzino tampone è riservato unicamente agli articoli strategici, che con la tecnica pull sono tenuti sempre alla giusta quantità. Il contesto è poi integrato dalle indicazioni visive, che permettono di avviare un processo di riapprovvigionamento più efficace.